By Matthias Kohlbrand In
New Assessments support Stable Production Processes
Production systems must work reliably according to their schedules in order to meet quality requirements and delivery deadlines. The real stability of the manufacturing process can be recorded and monitored using various process parameters and characteristics. The Cosmino software performs this task automatically. Employees will be notified only when a parameter stands out. For this purpose, Cosmino has a comprehensive inspection planning system. Threshold values can be stored for the individual values as well as for a spread range.
[caption id="attachment_10577" align="aligncenter" width="300"]
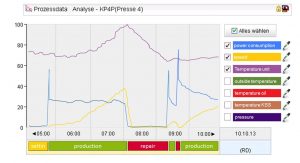
Fig.: Monitoring various system parameters ensures stable processes[/caption]
The Statistical Process Control (SPC) system is a manual approach to ensuring process stability and product quality using an inspection plan and frequent samples. The Cosmino software provides employees with support by automatically triggering inspection orders according to inspection plan guidelines. Based on the inspection results (measures), the software will determine the average, the standard deviation and check these against their control limits. Further, the process capability index (Cpk) ist calculated for the last 25 samples and displayed in the dialog. Optionally Cosmino can switch to 100%-Inspection if the minimum requirement for the cpk is not met.
[caption id="attachment_10580" align="aligncenter" width="300"]
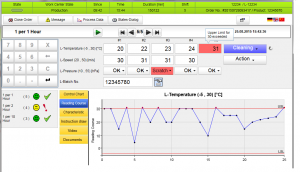
Fig.: The SPC dialog generates a control card and the Cpk value from the recorded samples[/caption]
In order to be able to guarantee quick intervention in case of instable parameters, trained maintenance personnel must be available around the clock. If this cannot be guaranteed, preventative maintenance measures can help avoiding unplanned losses such as technical breakdown. To determine proper inspection intervals, trends and changes in the process parameters must be observed and analyzed over the long term. The Cosmino DynaMon report tool depicts statistical key figures automatically in a standardized manner. Experience shows that only automatically generated assessments will in fact be used periodically.
[caption id="attachment_10426" align="aligncenter" width="300"]
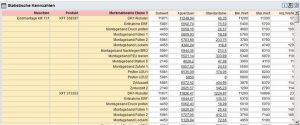
Fig.: Example of a key figure table[/caption]
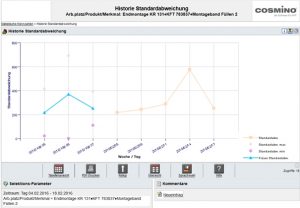
[caption id="attachment_10423" align="aligncenter" width="300"]
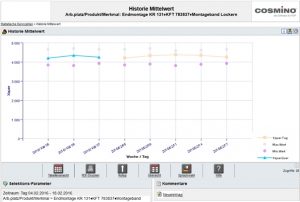
Fig.: History displaying the daily (yellow) and weekly (blue) average for each characteristic as well as the standard deviation[/caption]
Interactive Statistical Analysis based on Record Data
For the interactive statistical analysis of the recorded values, there are special programs which support analytical processes including data mining. If for example qs-STAT is being used, Cosmino data will be transferred to it through an interface with the click of a button or by a scheduled background process. Cosmino data can also be exported in XML format for processing by other statistics software. The R software (
www.r-statistik.de) is one free example. The Cosmino Service Team will be happy to provide support for any questions about exporting data into R. With the help of this statistics software, the data acquired with Cosmino can be analyzed and depicted as slices, box plots, pie charts, histograms, correlation matrices or similar representations. Abnormalities and relationships between individual process parameters can also be found in large databases and process stability optimized.
.
[caption id="attachment_10422" align="aligncenter" width="448"]
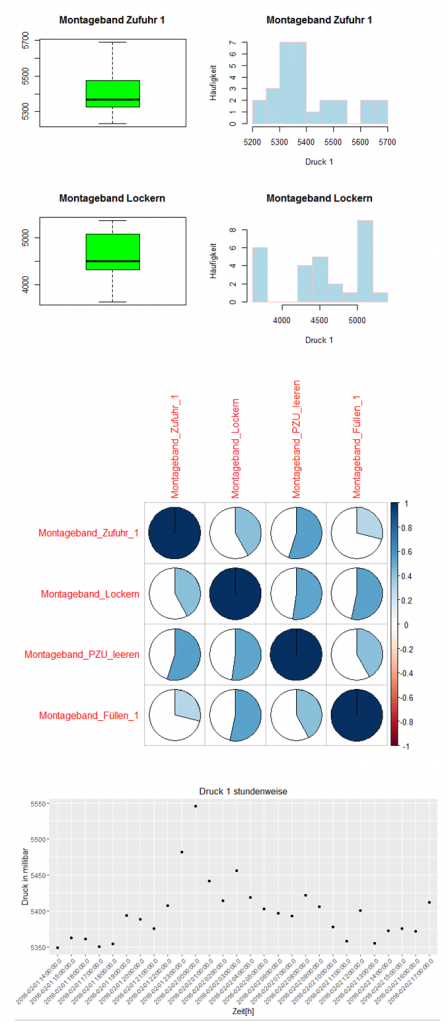
Fig.: A box plot (the circle indicates an abnormality), histogram, correlation matrix as a pie chart and a timeline[/caption]